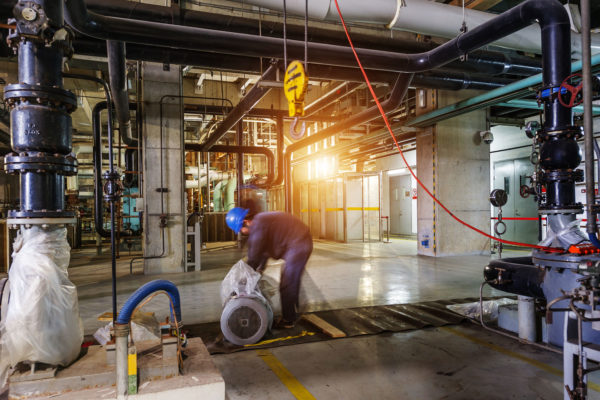
Novo foco estratégico na manutenção
Num ambiente de acirrada disputa pelos mercados, a produtividade representa um diferencial essencial, visando à sobrevivência e a perenização das empresas, garantindo o ritmo necessário para competir com os grandes players. Neste cenário, qualquer percentual mínimo de melhora no desempenho operacional pode significar posição de destaque da empresa em seu ranking de atuação. Assim, a manutenção representa, agora, ao lado da qualidade, da logística e da competitividade, uma ferramenta estratégica na consolidação das empresas vencedoras.
Se o trabalho começou com a manutenção corretiva e preventiva, a última década colocou a engenharia da confiabilidade e a manutenção preditiva como novas metas. A mera substituição de peças revelou-se ultrapassada e antieconômica. 0 monitoramento sistemático dos equipamentos permite maior confiabilidade e disponibilidade da infra-estrutura de produção, evitando paradas que comprometem os indicadores de produtividade e os prazos de entrega.
A mudança de conceito passou a exigir, na prática, tecnologias mais avançadas e mão-de-obra qualificada, já que a atividade deixou de ser vista como complementar; agora ela é vital para o desempenho operacional.
“Numa época de escassez de dinheiro para novos investimentos, a
assume um papel fundamental para preservar os ativos, elevando a sua disponibilidade e garantindo o timing da produção”, destaca o coordenador de Comunicação da Abraman, Rogério Arcuri Filho. Esta foi, aliás, uma das principais conclusões dos debates entre representantes de 26 países participantes do I Congresso Mundial do setor, realizado em setembro em Salvador, na Bahia.
O “Documento Nacional 2001 – A Situação da Manutenção no Brasil”, divulgado este ano pela Abraman, constata que em 2001 a manutenção movimentou um volume de negócios equivalente a 4,47% do Produto Interno Bruto (PIB), algo em torno de US$ 26 bilhões. O documento destaca ainda que, graças à melhora das técnicas adotadas, a disponibilidade da infra-estrutura operacional numa amostra de 142 empresas pesquisadas, incluindo o setor siderúrgico, petroquímico e de transportes, cresceu de uma média de 85,82% em 1997, para 91,36%, em 2001, havendo, inclusive, picos de 94,4%.
A fábrica de caminhões da Volkswagen, localizada no município de Resende, no Rio de Janeiro, que terceiriza 100% dos serviços de manutenção, submetendo-os ao controle de cinco engenheiros de seu quadro de pessoal, foi além dos resultados da pesquisa. “Fechamos o mês de outubro com uma disponibilidade de 99,92%”, informa Geraldo Ramos Nogueira, engenheiro de manutenção da empresa, justificando que houve apenas uma parada de dez minutos no período, e que, no cotidiano, a empresa dedica um turno à manutenção preventiva e outro à produção. De janeiro a outubro, a média de disponibilidade chegou a 99,31%.
A manutenção preditiva também integra a estratégia da Volkswagen. “Operamos não só com análise de vibração e controle termográfico. Adotamos também outras técnicas que nos permitem identificar o local e a intensidade do desgaste em determinados equipamentos, sem precisar abri-lo”, detalha Nogueira, destacando a importância deste trabalho para evitar paradas não-programadas e trocas desnecessárias de peças e máquinas antes de finalizar sua real vida útil. Os dados sobre o histórico do desempenho das máquinas, coletados pelas equipes de manutenção das oito parceiras responsáveis pelas linhas de produção, são analisados pelos engenheiros, que planejam as ações operacionais, coordenando os trabalhos terceirizados.
Em Cubatão, um dos destaques em termos de disponibilidade dos equipamentos foi alcançado pela Companhia Brasileira de Estireno, chegando a 95% em 2001, graças, também à manutenção preditiva adotada a partir de 1995. Porém, o racionamento de energia elétrica no ano passado derrubou esta média para 90%, forçando paradas pelo corte no abastecimento, relata o coordenador de Manutenção, Rui Gadelho.
“Esse tipo de manutenção aumenta a vida útil do equipamento e a disponibilidade da planta”, diz ele, ao explicar que o método adotado pela empresa contempla a análise de vibração dos equipamentos rotativos. Os dados apurados possibilitam um diagnóstico do comportamento operacional dos equipamentos, permitindo identificar a evolução de desgaste de rolamentos, de eixos, de falhas de lubrificação, de desalinhamento do conjunto rotativo e de outras peças. Além de manter a estrutura em funcionamento, a empresa vem obtendo a reduções de custos.
Os resultados da manutenção preditiva repercutem sobre o desempenho global da empresa, observa José Luis Pimenta, gerente técnico comercial da Monitek, empresa australiana com 12 anos de experiência no mercado internacional de manutenção, com filial no Brasil há um ano. Os dados da Abraman mostram, por exemplo, que as empresas pesquisadas estão obtendo mais rendimento de seus ativos em conseqüência do aumento da vida útil. Entre 1997 e 2001, a idade média dos equipamentos e instalações das empresas passou de 16 para 18 anos.
Um fato registrado na Casa de Pedra, mineradora localizada em Minas Gerais e que abastece a Companhia Siderúrgica Nacional, de minério de ferro, exemplifica a realidade constatada pela Abraman, conforme relata Pimenta. Um dos equipamentos da mineradora, com 29 anos de uso, tinha uma parada programada de dez dias, mas o monitoramento dispensou esse procedimento. A manutenção preditiva garante a operação da máquina por mais um ano, prazo que se completará ainda em 2002, coincidindo com uma segunda parada programada.
0 impacto da interrupção temporária das operações de uma empresa pode ser medido, segundo Pimenta, pelo valor dos bens que deixam de ser produzidos. Uma parada na laminação de uma siderúrgica, segundo ele, custa aproximadamente de US$ 30 mil a US$ 35 mil por minuto.
Considerando valores como estes, Pimenta afirma que os gastos com a manutenção preditiva são mais do que justificáveis. “Para cada dólar investido, o retorno médio é de US$ 12, mas pode chegar a US$ 70. Em seu primeiro ano de atuação no Brasil, a Monitek contabilizou um retorno médio de R$ 6,00 por R$ 1,00 investido.
O cálculo foi feito com base no lucro cessante verificado com uma parada de emergência evitada pelo serviço prestado, explica Pimenta. Essa metodologia pode ser adotada também para planejar a manutenção de máquinas e equipamentos numa indústria, com o objetivo de reduzir os custos de estoques.
Há casos em que um misto entre vários conceitos de manutenção pode assegurar resultados práticos surpreendentes. Foi o que ocorre, na fábrica de biscoitos da Bauducco em Extrema (MG), onde são realizadas manutenções corretivas, preventivas e preditivas. Roque Almeida Júnior, chefe de manutenção da unidade industrial, informa que a preditiva foi posta em prática há dois anos e meio, por meio da contratação dos serviços da Semapi Consultoria de Informática, e a mudança foi visível. “Até 1996, estávamos com um índice de disponibilidade entre 80% e 82%, quebras e paradas freqüentes. Recentemente, a disponibilidade passou a oscilar entre 95% e 96%”, diz ele.
A relação custo-benefício também é notável: o investimento inicial com essa modalidade de manutenção foi estimado entre R$ 18 mil e R$ 20 mil, enquanto a parada por uma hora de uma única linha de produção com capacidade de processamento de quatro toneladas/hora pode causar uma perda em torno de R$ 19 mil. Esta alternativa permite o levantamento de dados sem a parada do processo de produção, eliminando perdas com a inatividade. Mas uma não invalida a outra, pois são encarados como serviços complementares.
A melhoria contínua encarregou-se de introduzir na manutenção a chamada engenharia de confiabilidade, cuja gênese foi desenvolvida na Aeronáutica a partir do fim da década de 60. Um estudo realizado sobre o plano de manutenção do Boeing 747, avião top de linha da época, com tecnologia de ponta, mas com maior número de componentes do que as aeronaves anteriores, revelou que, se fosse realizada a ação clássica preventiva, com paradas para troca sistemática de componentes, a aeronave passaria mais tempo em terra do que no ar.
0 novo conceito introduziu o sistema de tarefa de detenção de falhas (TDF), testes operacionais e equipamentos de reserva, buscando não apenas preservar o componente, mas a sua função. Um dos objetivos é o de dilatar ao máximo a vida útil da peça ou equipamento e reduzir ao mínimo o número de paradas.”Esse conceito começou a ser adotado nos últimos sete anos por empresas de outras áreas, inclusive da indústria em geral, incorporando aspectos econômicos e financeiros, como a gestão de ativos, análise de depreciações e de rentabilidade”, revela Arcuri, da Abraman, lembrando que “confiabilidade e disponibilidade” são as palavra-chaves do processo.
As mudanças não devem parar por aí. Alberto Januário, superintendente de Manutenção da Usiminas, revela que a atividade está ganhando novos contornos. “Ela agrega valores, rapidamente, às questões estratégicas das organizações, como disponibilidade, confiabilidade, segurança operacional e pessoal, qualidade, preservação ambiental e otimização de custos.”
“Para a Cosipa, que possui certificações nas áreas de qualidade (ISO 9001/2000 e QS 9000), meio ambiente (ISO 14001) e saúde e segurança (OHSAS 18001) e que investe em modernizações com alto grau de automação, no qual a complexidade dos equipamentos e sistemas é cada vez maior, cria a constante necessidade de atualização do corpo técnico para a execução das tarefas e a aquisição dos meios adequados para a sua realização”.
Gestão do almoxarifado
Dentro do novo conceito, a gestão do almoxarifado também é uma variável importante, pois, além de controlar a entrada e saída de peças de reposição, pode manter estoques menores, reduzindo a pressão dos custos financeiros decorrentes da mobilização do capital investido em compras. Vale ressaltar que, com os níveis de taxas de juros praticados no Brasil, qualquer economia de capital de giro beneficia a competitividade.
Esse raciocínio determinou, em parte, a aproximação entre a indústria automobilística e seus fornecedores, os chamados sistemistas (empresas prestadoras de serviços localizadas próximas às montadoras), juntando o just in time com a eliminação de estoques elevados, garantindo eficiência operacional, logística, financeira e de manutenção. Os dados disponíveis revelam que o impacto dos estoques de segurança sobre os custos de manutenção das empresas no Brasil passou de 16% em 1997 para 11,95% em 2001. Da mesma forma, a rotatividade média do estoque diminuiu.
No limite, o serviço foi transferido para os fornecedores de peças de reposição, os quais operam do outro lado do balcão, ou seja, prestam serviços de manutenção, como terceirizados. É o caso da OV Rep Comércio e Representações, de São Paulo (SP), que começou a operar em 1988, aproveitando o nicho que se abria, em pleno governo de Fernando Collor de Mello.
0 seu foco é o das engrenagens industriais e acoplamentos flexíveis para a área mecânica e o desafio é ter cada vez mais agilidade na prestação de serviços e prazos de entrega curtos para compensar os custos de estocagem.”Começamos a montar estrutura de estoques a partir de 1994, quando as empresas passaram a transferir essa responsabilidade para os fornecedores. Os custos financeiros são muito altos”, revela o diretor-técnico e comercial da OV Rep, Orlando Vulcano Júnior.
Outro teste de resistência, segundo ele, é satisfazer e fidelizar os clientes, com níveis de suprimentos razoáveis, mesmo com retração de vendas em torno de 40% como ocorre agora, em comparação com movimento de 2001. A solução encontrada foi reduzir os estoques em um terço, mantendo a margem de segurança para não perder cliente por falta de atendimento.
A qualidade da mão-de-obra e estrutura hierárquica das empresas que operam em manutenção também vêm sendo impactadas pelas necessidades do mercado e pela evolução tecnológica. “Quanto mais capacitada e treinada a equipe, menor será o tempo de parada e o custo de manutenção”, assegura o gerente da área de Marketing Phoenix Contact, Valter Pavani. A empresa fornece equipamentos de conexões e interfaces em informática, respondendo por 30% do mercado brasileiro na área industrial, e presta serviço de treinamento de técnicos especializados para seus clientes.
Otto Padilha Kossling, gerente Manutenção da Companhia Santista de Papel, diz que alguns equipamentos exigem conhecimentos diferenciados do operador, lembrando que a familiaridade com atividades específicas pode propiciar a troca de informações sobre novas tecnologias, aprimorando os resultados operacionais e aumentando o valor agregado na produção.
A demanda por especialização da mão-de-obra é maior na manutenção preditiva. Por mais simples que seja o equipamento, o operador tem de conhecer a linguagem do programa do computador para poder analisar adequadamente os dados colocados à sua disposição, alimentá-lo com novas informações, planejar e adotar decisões rápidas e de forma autônoma.
Felizmente, a realidade está caminhando neste sentido no Brasil, segundo dados da Abraman. Entre 1995 e 2001, o percentual de pessoal técnico especializado ocupado em serviços de manutenção cresceu 37%, enquanto os quadros de nível superior cresceram de 6,65% para 7,64%. A variação da mão-de-obra de nível médio subiu de 13,52% para 14,81%.
No total, gastou-se mais com pessoal, já que os custos da folha salarial de manutenção passaram de 57%, em 1995, para 61%, em 2001. A manutenção tornou-se uma atividade mais próxima do chão de fábrica. Em 1995, 86% dos serviços estavam vinculados à diretoria e à superintendência; em 2001, o percentual caiu para 61%.
Há dez anos está em prática no Brasil o Programa Nacional de Qualificação e Certificação de Pessoal de Manutenção (PNQC) por iniciativa da Abraman em parceria com o Serviço Nacional de Aprendizagem Industrial (Senai). Até setembro deste ano, foram certificados 3.052 trabalhadores, entre caldeireiros, montadores, eletricistas, mecânicos, instrumentistas, instaladores e reparadores de linhas de acesso.
Os resultados do programa em relação ao universo da mãode-obra de manutenção ainda são pequenos, mas estão crescendo. Em 1997, apenas 4,3% de técnicos eram certificados pelo PNQC. No ano passado, o número subiu para 7,02%. Em 2001, o currículo continuava sendo a principal ferramenta de identificação da qualificação, abrangendo 31,58% do pessoal ocupado, enquanto 29,12% foram treinados internamente pelas empresas e 18,95% por terceiros. No total, 55,1% tinham qualificação e o restante estava sem qualificação no setor.
Nenhum comentário